Experience Matters
You can filter your search by typing in an employer name, or selecting a major. This is a great way to see what possibilities are out there!

NSE Product Engineering
Caitlyn
Major: Mechanical Engineering
I worked on two of the high-speed NSE drills, the Core-U Drill and the Sumex Drill. Both drills contained rotor issues in which solutions were implemented.
The Core-U Drill rotor contained an issue during the assembly of the balance rotor. When the front balancing ring, which is the last component pressed onto the rotor assembly, was pressed, a bur would form due to the misalignment. The front balancing ring was a softer material than the rotor; as a result, a majority of the bur's material was from the front balancing ring. This bur was being formed 30% of the time, causing a slip fit bearing to be unable to be placed onto the rotor for balancing. One this occurred, the entire order would need to be placed into rework until the situation was corrected. My project was to develop and test solutions that would reduce and hopefully eliminate the bur formation issue. Throughout this project, I worked in Minitab and Pro-E to develop DOEs and Rotor Assembly Blanks for testing. There are two possible rotor changes and three possible front balancing ring changes. For the two styles of rotors, a chamfer of 75 degrees was added for the first style, and a radius of 0.0035 for the second. For the front balancing ring, a vibratory finish, Loctite 680, and a combination of the two were added to the different styles. A total of 12 combinations were tested, including the control group. These test results provided feasible solutions for preventing the problem in the future.
The Sumex Drill was the highest scrap and warranty product of the NSE division. For this project, I was required to discover and implement a solution to fix one of the larger drill issues. After looking at the complaint trending information and the fishbone diagram that I created, I was able to find that there was a large number of complaints involving the balanced rotor assembly. The rotor shaft drive groove would contain an increased depth after repeated use of the routers with the footed attachments. The rotor shaft drive groove is the area where the rotor comes into contact with the router when a footed attachment was used. The router in the attachment was a harder material than the rotor causing the rotor material to compress form to the shape of the router's contact end. This increased depth created an increased gap between the router and the footed attachments, which impended the craniotomy that was going to be performed. In order to solve this issue, a carbide plug was added to the rotor shaft drive groove area. This solution was found through research performed by the new product development department. For this change Pro-E and PTC Change Request systems were used. I created the changes that were required in the rotor and worked on creating a fixture for the carbide plug to be pressed into the rotor in Pro-E. I also began a Change Request in the PTC system.
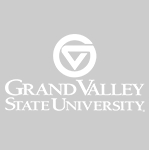
BISSELL co-op 2nd Term
Tony
Major: Mechanical Engineering
I was given two large projects to work on this term, and was given more control of the projects than I was in my first term. The two projects involved a lot of statics knowledge, along with CAD design, and a little bit of dynamics/fluids understanding.
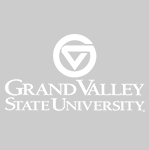
Trane BAS Internship
David
Major: Mechanical Engineering
I had the opportunity to work on graphics for each job. Through the use of Photoshop, I created floor plans, where I then inserted the components, such as air handlers, VAVs, heaters, and coils. The components of the air handlers and water systems were also created in Photoshop, which would be later used as the basis for the building controls in Summit and SC automation.
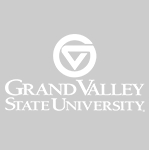
Mechanical Engineering Internship
Jake
Major: Mechanical Engineering
On any typical day, I was exposed to constructing drawings, Bill of Materials, setup sheets, process management, prominent customer interaction, developing presentations, and answering floor workers questions.
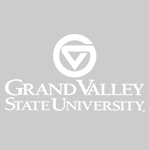
Oliver-Tolas Healthcare Packaging: Second Term
Spencer
Major: Mechanical Engineering
I was involved with the installation and qualification of several new pieces of machinery as well as product and process qualifications. This involved a lot of hands-on work performing testing on the new equipment, and a small amount of report/paperwork preparation and routing. Notably, I was responsible for the installation of a radioactively sourced gauging system used to determine the thickness of finished products. This project entailed designing the hardware necessary to mount the system, working with Plant Services to make the appropriate preparations for installation, and working with the device manufacturer's Engineer to install and set-up the system. Beyond this, I was responsible for all of the testing necessary to demonstrate the devices functionality and report my findings to my superiors.
Read More About Oliver-Tolas Healthcare Packaging: Second Term
From Sheets of Metal To Finished Product
Husam
Major: Mechanical Engineering
I was assigned project manager on some of the main projects that DeWys had at the time I started my co-op. Working as a project manager gave me the opportunity to experience every aspect of a manufacturing company. It improved my understanding to the process from the beginning until the product is finished and shipped to the customer. During my co-op I had many tasks and problems to solve, but basically I was coordinating everything that was going on for the project and ensure problems are solved.
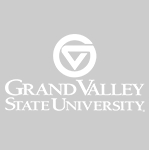
Mechanical Engineering Co-op term 1: BISSELL
Tony
Major: Mechanical Engineering
I worked in product attributes, which meant I was given many different tasks from many different engineers. This was nice from an experience gaining standpoint, because it meant that I got a fairly broad taste of the industry fairly quickly. I did a decent amount of work in Pro-E and ANSYS, and spent a lot of time running tests and helping out with different design projects.
Read More About Mechanical Engineering Co-op term 1: BISSELL
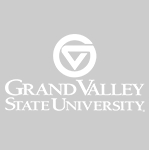
Intern Mechanical Engineer for second co-op
Marcus
Major: Mechanical Engineering
I was assigned to help start a new project line called the Infineon/Sonoma/IVC part. This part essentially controls the timing of the cams in your car. I started prototyping and slowly began to automate my process through the help of robots, bowl feeder, pneumatics and conveyers.
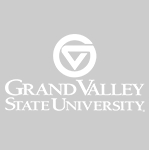
Johnson Controls Manufacturing
Matt
Major: Mechanical Engineering
I was an on call manufacturing engineer in one of their major plants in Holland. I solved critical issues on the line that prevented manufacturing and helped to prepare for a launch of a major door panel line. I also was given 3 other lines to manage where I was the sole manufacturing engineer where I had to manage engineering changes, solve issues, and make the jobs of the operators efficient and simple.
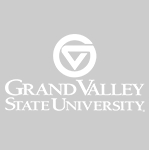
Intern Mechanical Engineer
Mark
Major: Mechanical Engineering
My tasks and projects got more difficult as the semester went on. On my first day I was involved in disassembling of some robotic stations, but after that I learned at an accelerated rate. My first project was to create a pneumatic system the would decide if the part went into a bucket of continued down the assembly line. This task seemed overwhelming at first, but after asking some questions and making some mistakes I learned how to complete the task. My projects then got harder. My next project I was assigned was "make the robotic test table work". I had not idea, but after watching the station run and figuring what was causing the issues I was able to correct the problem.
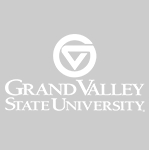
Second Semester Engineering Co-op
Austin
Major: Mechanical Engineering
I supported the service team, production team, cabinet engineers, refrigeration engineers, and electrical engineers in their everyday tasks. For our engineers, I helped model assemblies in our CAD software, updated refrigeration and electrical schematics, put together bills of materials, released jobs to production, documented engineering/sales changes, and did projects to help improve our processes.
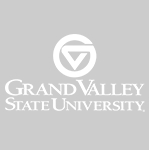
Co-op at Koops Inc.
Michael
Major: Mechanical Engineering
I worked as a mechanical engineer designing machines. I designed multiple machines for the automotive industry.
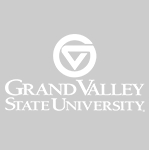
Engineering Intern
Conlin
Major: Mechanical Engineering
Assisted manufacturing, design, quality, and engineering with whatever they needed. This involved mundane tasks such as creating and updating documentation to buying and designing machinery to improve current processes.
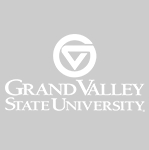
UCC Engineering Co-op
Taylor
Major: Mechanical Engineering
I worked on industrial projects. Some projects I managed include a cooling water system and a water filtration system among many others. The water filtration system required fluid mechanics calculations and pump system design. I also gained project management skills as I managed the project and the project budget myself.
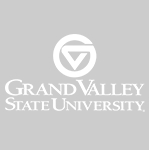
JR Automation 3rd Rotation
Dan
Major: Mechanical Engineering
-Design automation machinery based on customer needs using 3D CAD software
-Detail and check 2D drawings for manufacturing
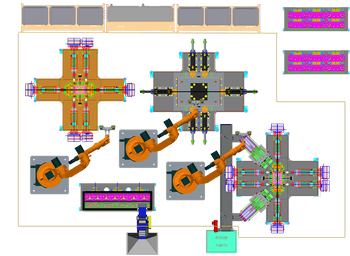
Third JR Co-op Finishes Strong!
Matthew
Major: Mechanical Engineering
This semester I worked in the quoting department at JR Automation. I worked with multiple quotes all in the hundred thousand ranges and a few ranging in a couple million dollars. I worked with some quotes that have come back for a new quote and some that have been passed around without any firm grounding for the most part. Some of the quote I developed concepts from ground up and devised cost worksheets reflecting the anticipated costs plus the margin of gain JR looked to make.
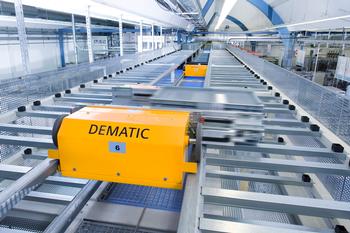
Dematic Co-op Term 2
Jillian
Major: Mechanical Engineering
As a mechanical application engineer, I was on team that were the middlemen between our R&D department and the customer. Mechanical applications implements all of the product Dematic offers to accommodate the customers needs. We design the layouts of equipment, order all of the things needed, and then go to the job site and ensure everything is working properly before handing it over to the customer.
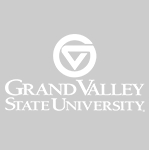
TBVC co-op rotation 2/3
William
Major: Mechanical Engineering
About half of the time I spent working in different departments such as quality lab, chem lab (making rubber), cost estimating and purchasing, assembly, test lab etc. The second half of my internship, I spent taking on the role of a project engineer. I created and followed work orders, and analyzed test data.
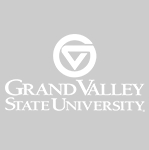
Co-op 2: New Product Development
Colton
Major: Mechanical Engineering
I helped in the process of a new product launch, which involved creating CAD parts, assemblies and drawings. It also required me to have prototypes constructed and tested in order to verify fit and function. I also worked on a product redesign, which was meant to be a cost savings project for the company.
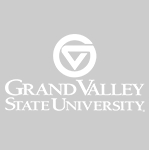
My Summer in JCI Interiors
Matt
Major: Mechanical Engineering
I performed a study on the pressure inside of an injection mold during pack. This will allow the tooling department at JCI to better predict which size molding machine door panels will fit in. This can result in more business won by cutting costs to the customer, and more profit since we can put bigger door panels in smaller machines.
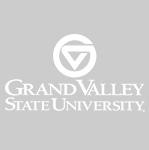
Process Engineering Internship
Andrew
Major: Mechanical Engineering
This summer I spent a lot of time doing different design work as well as hands-on building work. As far as the design work I did, I did things such as designing nests for parts to be held while different tests are done on them. I designed nests to hold some blind spot indicators that go in the outside mirrors of a car as well as several nests that hold entire mirrors while they are tested for the amount of torque that it takes to move the mount of the mirror. I also spent some time designing a vacuum system that deposits backings from a glass element into a trash can. When these backings are peeled off of the glass, they are very statically charged and stick to many different things including clothing causing a big mess. The system that I designed takes these liners and sucks them off of the operators hand and down into a trash can below, eliminating the mess that was caused before. I also designed several flow racks to present the material in better ways to the operators on the line and also got to build these flow racks in the tool room as well.
There are many other projects that I worked on over the summer as well, these are just a few but overall it has been a very rewarding experience with a lot of good and challenging projects to work on.
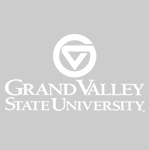
Co-op #2 at JR
Daniel
Major: Mechanical Engineering
I worked at a mechanical engineer checking machine drawing packages, detailing packages, and even designing parts for automated machines.
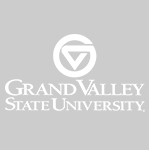
Trans-Matic Engineering
Benjamin
Major: Mechanical Engineering
I was tasked with making sure the tooling drawings were up to date. I also spent half the semester on gage design. Gages are used to make sure the incredibly intricate parts are accurate to within 1/1000 of an inch.
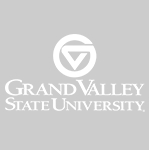
GVSU 3rd and Final Co-op W15' Semester
Cody
Major: Mechanical Engineering
During the current semester I completed tasks related to advanced product development and product engineering. At Magna Mirrors in Holland I work mainly with the Inside Mirrors Division. I was involved with some design work and prototyping for the development of new products. I would often be asked to make prototype mirrors either for testing or customer samples. I was also involved with Root Cause Analysis for determining the root causes of problems with specific products. There were some projects that required designing fixtures or components using SolidWorks software, that would aid in the testing, development and manufacturing of products. I often would work with engineering staff to maintain programs: DFMEA's, DVP's, BOM's, benchmarking, design review checklist, tolerance stacks, drawing GD&T, DFM/DFA checklists and any other specified requirements.
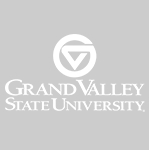
Second Co-Op At Innotec
Matthew
Major: Mechanical Engineering
The majority of my time was spent being production responsible. This entitled startup, shutdown, correcting machine stoppages, correcting machine errors, assisting manual process personnel, assembling boxes, cleaning the area, filling materials for production, reworking in process production parts, IMM tool changes, IMM cover changes, quality checks, and a whole other number of day to day issues.
When not being production responsible my two other main tasks were to monitor internal scrap / rework and spare parts levels. The scrap / rework responsibilities included formulating reports for the daily, three day, weekly, and monthly numbers, doing all rework for product that was unable to pass manual inspection, and alerting team members of any spikes or changes in internal scrap / rework.
The spare parts responsibilities was very straight forward. I was responsible for reordering any spare parts used in the day to day operations of the production area. I was also responsible for researching any parts needed for projects being done by fellow area members. I was responsible for getting the best price possible and keeping needed parts on hand. I would have also like to re-organize and set up a tracking system for the spare part storage areas, but this was not possible due to the large amount of production and other responsibilities.
The remainder of my time was spent fixing daily problems that occurred with production machines. I worked on a number of items through out the course of the semester:
- Bezel IMM Feeder
- Housing IMM Feeder
- Housing Circuit Pick And Place
- Housing Part Feeder Bowl Improvements
- Housing LED Install Improvements
- Bezel Feeder
- Bezel Finished Product Tote Stacker
- Reflector Scrap Track
- Circuit Die
- Making new production and area announcement boards
All of these "projects" were small items that were only addressed when production was stopped or interrupted as a result of that particular station being broken or malfunctioning. Some other small improvements dealt with wiring and fixing transfer problems. Overall, production was far more important and took priority over everything else.
All opinions, conclusions or recommendations expressed are those of the author(s) and do not necessarily reflect the views of GVSU.