Experience Matters
You can filter your search by typing in an employer name, or selecting a major. This is a great way to see what possibilities are out there!
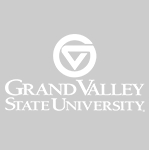
JR Quoting Intern
Ben
Major: Mechanical Engineering
I quoted material handling cells that would use robots to move parts around and torque bolts to a certain specification. I quoted mold tending cells with robots that would retrieve molded plastic parts from and injection mold machine. I quoted assembly stations that would verify the operator assembled a part correctly.
JR has a vast customer base and there were very few quotes that were alike.
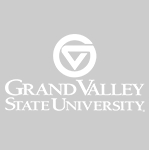
Real World Engineering
Caleb
Major: Mechanical Engineering
While my time at this company, I was able to work first hand on the automated equipment. I was able to troubleshoot problems, ensure proper assembly of the parts and overall prove out of the machines. I was also able to install, power up, and service the machines that this company put into factories.
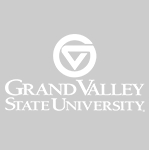
Mechanical Engineer Co-op
Jared
Major: Mechanical Engineering
AutoCAD, ELMII, and SMM were all software (some developed by Dematic) used to create a layout for a customer, order it, track it to the site, and observe it being built.
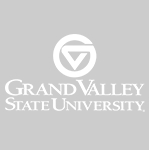
First Co-op: Quality Control
Kyle
Major: Mechanical Engineering
I performed calibrations on tooling as well as measuring equipment. I helped convert from an old tool maintenance database to a new more professional database and wrote all new work instructions on how to calibrate each set of tools that was stored in their ISO standard. I also helped do a return on investment project to help determine if a new program would be worth the investment.
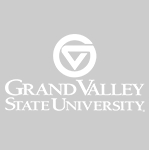
Genesis Seating Co-op Experience
Leif
Major: Mechanical Engineering
My main task at Genesis Seating was to design and create assembly fixtures and part carts. I would be given a problem that the floor workers are experiencing and would have to come up with a way to solve that problem. Most of this just entailed designing a fixture that would hold the part being worked on in a certain orientation. I was also task with doing time studies. This is a way for Genesis Seating to make sure what they quoted a company for labor cost was correct. I would simply watch the work assemble a chair and record the time it took he/her.
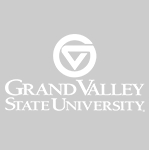
Genesis Seating Co-op Experience
Leif
Major: Mechanical Engineering
I was responsible for designing continuous improvements. I designed, and constructed, many material presentation carts and racks for the work cell to use. Another large project I worked on was a quick lift table. Most pneumatic lift tables take many seconds to raise and lower. I had to design a lift table that could lift a chair in 3 or 4 seconds. I accomplished this by the use of an airbag jack that can inflate quickly with the right pressure of compressed air.
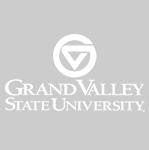
Stamping Matters
Andrew
Major: Mechanical Engineering
I created a 10" riser in SolidWorks that closes the shut height of a press. I also drew up concepts for a feeder to feed two coils of steel into a press at different speeds.
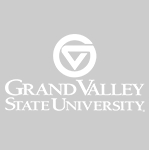
1st Co-Op Semester
Erik
Major: Mechanical Engineering
Many of the tasks and project that I worked on involved becoming familiar with the machines and manufacturing processes that are used to maintain part quality. This included working with machine operators, checking part dimensions and aiding in capability studies, and working on preventative maintenance sheets. I also worked on two different projects that helped reduce the number of parts damaged by the wash machines (used to remove chips, oil and other debris from parts).
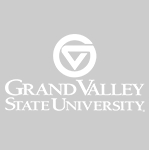
GHSP Intern
Zachary
Major: Mechanical Engineering
The tasks that I completed consisted of sound testing, creating and editing tolerance stacks, creating and editing bill of materials, designing and building prototypes, conducting independent studies of parts and issues associated as well as many more tasks.
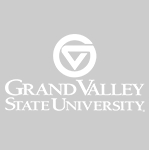
Haworth Engineering Internship -Brian
Brian
Major: Mechanical Engineering
I was involved in cost reductions, quality issues, and new product launch.
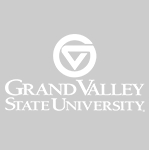
Haworth Inc.
Colton
Major: Mechanical Engineering
I worked on many engineering drawing updates and part model updates using ProE. I helped to construct, then run tests on Haworth's newest desking system. I worked on consolidation and quality control for different parts. I also worked on conceptual designs for a table leg.
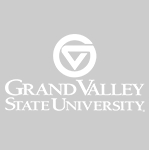
A Semester At JR Automation
Daniel
Major: Mechanical Engineering
This semester I worked as a mechanical engineer in the design department. I was tasked with various problems that I would have to develop and design, using PRO Engineer design software, a solution for. These problems varied from issues that had arose from machines that had been in operation for a few years to design new technology that was being implemented for the first time.
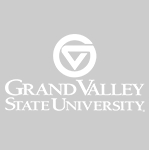
Cost and Concept Development Engineer
Erik
Major: Mechanical Engineering
Been working on creating quotations for different automation projects in a variety of fields.
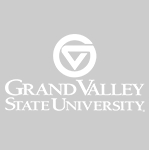
Engineering in the Motor City
Andrew
Major: Mechanical Engineering
Working in the design department, I was responsible for designing pistons, bearings, piston rings, and connecting rods. I also created drawings related to these 3D models. I worked closely with other engineers from related companies such as Ford, GM, an Chrysler.

Co-op Round #1
Prisciliano
Major: Mechanical Engineering
Being the first co-op, I started with some smaller tasks but was quickly brought up to speed. I started with prototyping possible new products and getting familiar with the injection machines and their programs. Shortly after this task was complete, I started building components for an entirely new production line. The line consisted of welders, inspection cameras, and component assembly robots.
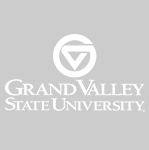
Padnos Co-op 3rd Semester
Jason
Major: Mechanical Engineering
I was able to experience every aspect of a project at Padnos; from meetings, field measurements, design, fabrication, installation, and follow-up improvements. This included coordinating with on-site supervisors, scheduling meetings, design, overseeing fabrication and installation, and following up post-installation with supervisors. This role carried through many projects including a vibratory shaker installation underneath a shredder mill, conveyor rebuild, access deck/stairs/ladder installation, an over belt drum magnet for ferrous material removal, and many more.
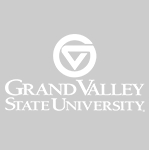
Fisen Co-op
Tyler
Major: Mechanical Engineering
I worked on standardizing a modification so that when a job comes up with it, all the engineering is done beforehand. In doing this project I had to complete a few different tasks. These included 2-D and 3-D modeling, Electrical drawings, talking to vendors, and creating documents needed for sales. I also had the chance to help on the production floor installing modifications.
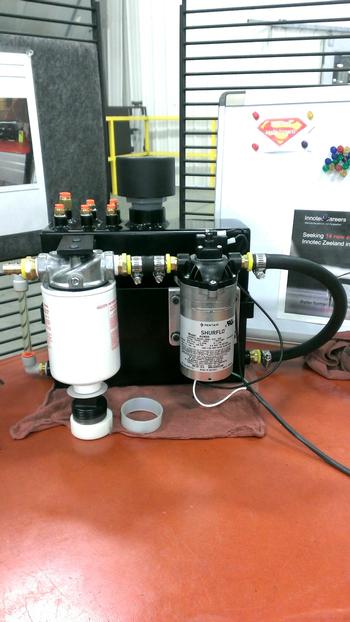
Learning the Skills
Kyle
Major: Mechanical Engineering
My projects were based on increasing the efficiency of the assembly line I was assigned to. During this work experience I designed an automatic oiling and filtering system that replaced an operator that manually filled and filtered the contaminated oil. I installed and fabricated a carrier steel straightening system that prevented 50 weekly interventions and 2.4 hours of downtime. I participated in many small installations around the line that increased production by 20%.
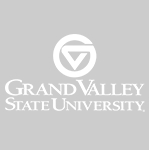
Dematic Co-Op: Final Rotation
Jillian
Major: Mechanical Engineering
This semester I was given the amazing opportunity to go to Europe for 2 months of the semester. I was there to ensure install of two sites went smoothly and turn the distribution centers over to the customer. I went to both Milan, Italy and Lille, France. When I returned, I worked on wrapping up the projects from the engineering side and turning the projects over to customer service. The rest of the semester I devoted my time to working with engineers to start up a new distribution center in Maryland. I was offered a job with Dematic before I left for Europe, so I have been learning more of what I will be doing when I start full-time after graduation.
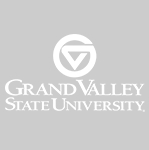
Automotive Crash Testing at Shape Corp.
Stephen
Major: Mechanical Engineering
I developed 2 LabVIEW data acquisition programs according to the needs of the tech center. One program is a strain gage data collection program that instructs the user how to mount strain gauges and will record data for up to 7 strain gauges at a time. I designed and built the software and some hardware for this project. I also got a lot of hands-on experience in a machine shop. My projects required me to use a manual mill, drill press, saws, and other equipment. I performed a lot of daily tests with the testing team including; dynamic vehicle crash tests (pendulum, flat barrier, IIHS, offset barrier, etc), pedestrian protection tests, dog bone and hardness material tests, and more.
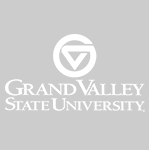
Lab Intern
Joshua
Major: Mechanical Engineering
The testing of the incoming steel to ensure that the coils are what the suppliers claim it will be.
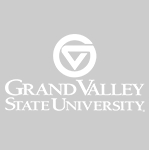
Stryker Instruments Co-op
Caitlyn
Major: Mechanical Engineering
During this second co-op experience, I worked with the Stryker Surgical division within R&D. I developed and designed a fixture in Pro-E to aid in the testing of a power drill used within knee and hip replacement surgeries. I investigated and implemented an ergonomic design for the fixture to provide a safe testing environment for developers and consultants. This design was tested and improved with the input from the Surgical R&D team. I researched and implemented electronics and a data acquisition system to obtain quantitative data on the drill throughout testing. Throughout this internship, I was also able to see the project through from beginning to initial testing.

TBVC first rotation co-op
William
Major: Mechanical Engineering
TBVC implemented a great co-op program for me in which I worked in each department before becoming an engineer. I started molding and assembling parts to get a good understanding of the fabrication process. I then worked in the test lab to better understand the different types of tests that can be performed. I finished the semester working in the chemical lab where all the rubber is produced. This is my first of three semesters at TBVC and I will begin design projects my next semester.
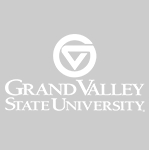
Best Mechanical Internship
Erik
Major: Mechanical Engineering
Got to be a part of a machine design team that takes requirements and specifications from customers and create machine solutions for them in CAD. I have gotten to experience starting small projects and working by myself but also being part of a group for greater projects. My work has involved 3D design in CAD, checking other designers work for errors and mistakes. Also gotten the opportunity to work with builders and make modifications on existing machines.
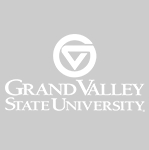
First Co-Op Semester At Innotec Corporation
Matthew
Major: Mechanical Engineering
The vast majority of my semester experience was focused on learning production and running the production lines (being machine responsible). I was machine responsible for an average of over 30 hours per week for the semester. The responsibilities associated with this were keeping production running no matter if it involved the clearing a simple error to tearing apart a station to replace a component which had ceased to function properly.
My next biggest daily responsibility was being in charge of ordering spare parts and parts needed for production line changes or improvements. This was very challenging since most orderable parts used on the machines were not documented and required research and price comparisons before ordering.
The remainder of my time was spent working on projects to help improve the production process. Some of these are listed and briefly described below:
Circuit Press Oil System: Updated current automatic oiling system, rewired panel, and updated company logic based software.
Finished Goods Stacker Extension: Finished goods tote auto-stacker was extended to allow for more tote capacity. Along with this the entire E-stop system was rewired and updated.
Finished Goods Stacker Re-alignment: The rails used for stacking the finished totes needed adjustment to prevent failures for totes both entering and leaving the system.
Line Capability Improvements: A second Power/Reset/Go setup was added to production lines along with a second monitor and mouse station. This allowed for faster machine failure fixes by eliminating the need to walk around the production line to restart a machine.
Additional Printer & Label Redesign: A printer was added to the production area so that label printing could be performed without the need for walking back and forth across the plant. Along with this change, a complete label redesign was needed for functionality with a new program.
Various Small Tasks: Changes to the company based machine logic software, addition of sensors, and other small engineering changes were made throughout the semester in order to improve production capacity and time between machine failures.
All opinions, conclusions or recommendations expressed are those of the author(s) and do not necessarily reflect the views of GVSU.